A new design of blade structure and slip ram to optimize CT BOP comprehensive performance.
The Gulf of Mexico oil spill in 2010 was a devastating disaster which caused 2000 square miles of pollution and 20 billion dollars of massive compensation. This was a warning to the well control equipment manufacturers about product safety and reliability and performance.
Coiled tubing blowout preventers are key for well control. It functions as the last protection to prevent the uncontrolled flow of liquids and gases during operations by having the ability to shear the coiled tubing and seal the wellbore simultaneously in case of any issues during the operations. Activating the slips prevent coiled tubing from falling into the wellbore, while the shear ram cuts the tubing, insuring the tubing staying in the BOPs until operations can be altered. The performance and capability of the shear ram and slip ram are the core technologies of a BOP. As the job location and working condition changes all the time, how could R&D engineers improve the efficiencies of the BOP performance? Below is the solution from Jereh R&D engineers.
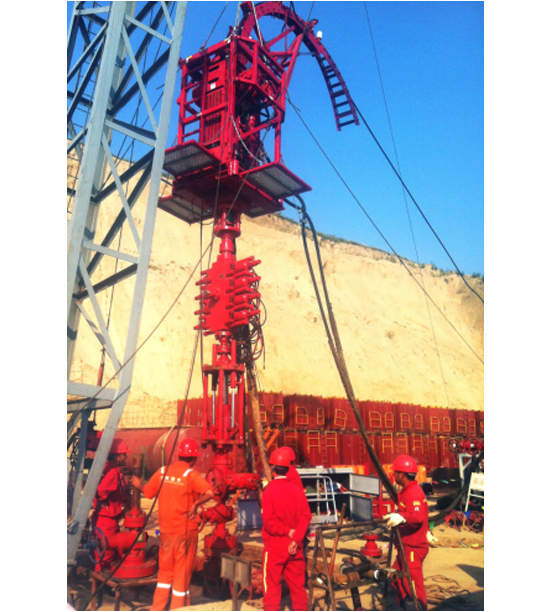
Figure 1: Jereh BOP
The force borne by the shear blade changes in a complicated way, which is what engineers have studied and improved on. At present, the shear stress is calculated based on material mechanics. However, people fail to take such factors as shear blade structure, blade clearance, shearing speed, friction and shearing section deformation into consideration. Therefore, material mechanics cannot reflect the nature of deformation during the shearing process.
To lower the shear force, Jereh engineers, through comprehensive analysis, calculation and verification, upgraded the full edge blade to an embedded structure to allow the CT to be sheered by using only 75% shear force.
Taking 2”Coiled Tubing (CT110, 0.204”) for an example, by studying on the material and heat-treating parameters, each blade is capable of shearing continuously 40 times, which greatly improves the shear ram performance.
The slip ram is at the same level of importance as the shear ram which serves to grab and hold the CT by latching shear teeth onto tubing hydraulically to prevent slippage. Since the CT will be damaged to a certain degree when the teeth are latched into the tubing, improving slip ram capability by minimizing the CT damage is another challenge to the engineers. The slip gripping angle, height, interval and heat treating affect the slip ram performance in different degrees. Through combined design calculation and verification, it is concluded that the obtuse-angled teeth can effectively hold the CT with minimum damage to CT and reduces stress concentration during heat treating to avoid tooth break. Still taking the 2” Coiled Tubing (CT110, 0.204”) as an example, the carrying capacity of the slip ram after optimization is 70.2tons.